CONCRETE SEGREGATION
- P-Concrete
- Apr 10, 2020
- 3 min read
Updated: Sep 30, 2020
How many times in dismantling a formwork for a fair-faced concrete structure have you found a wonderful surprise? Something like a big gravel concretion aka honeycomb. I assume you did the following, just in that order:
Give place to a comprehensible burst of anger
Blame it on the concrete as for its poor quality
Fix the problem finishing the gravel with a patch of mortar
…. eventually complaint with the concrete manufacturer asking for the money back.
Yet the problem is more serious than it seems, and the responsibilities are not as unique as they seem.
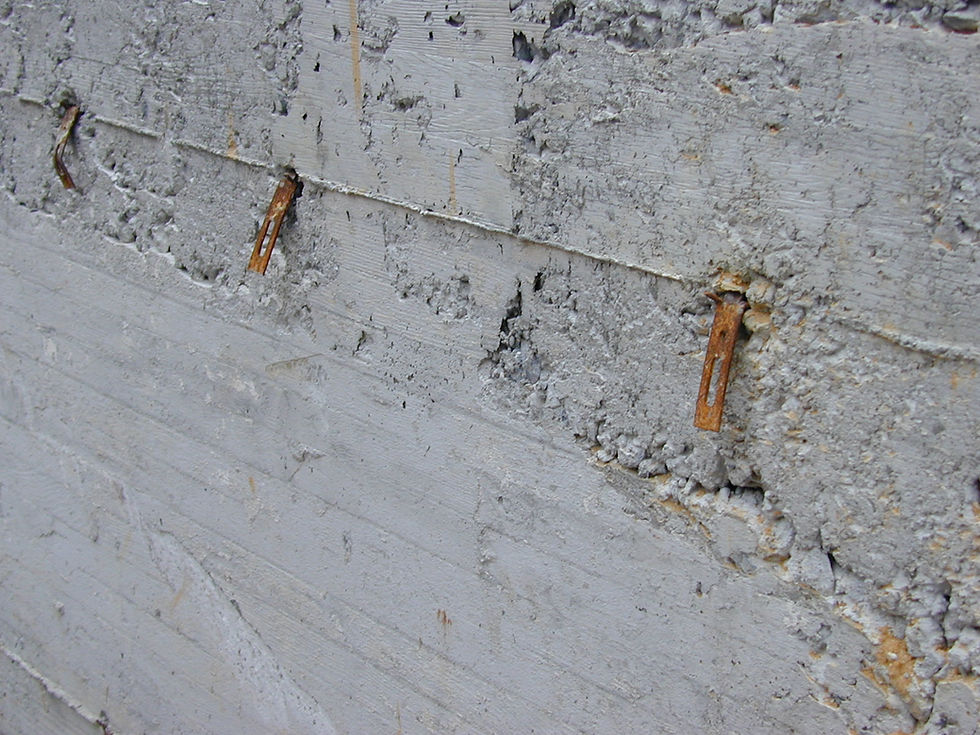
WHEN THE CONCRETE IS THE CAUSE

Concrete is a conglomerate, a sort of artificial stone, made up basically with cement, water, sands and gravels. All these components have physical characteristics deeply different and needs appropriate design to live in a single product in a homogeneous and cohesive way. When the concrete mix design tends to foster gravels, segregation phenomenon is more likely to appear. The same happens as per high water/cement ratio.
Another phenomenon known as “balling” contribute significantly to exposed gravel concretion. They are real balls of concrete, agglomerates which consists of a shell of hard cement paste with a content of very wet sand. They tend not to break, not even in the casting phase and they get stuck between reinforcement bars. This constitute a real obstacle to the free flow of fresh concrete and ends up with segregation phenomenon.
WHEN THE CONCRETE IS NOT THE CAUSE
Was the concrete consistency choice correct? (please read more in my post “Workability of concrete”) It is always better to choose fluid, superfluid if not even self compacting concrete (please check my post “Self Compacting Concrete”) they will be more easily set in place and, due to their design, have lesser chance to fall into segregation, while “stiff” concrete must be compacted thoroughly; the problem with low workability is that insisting with vibrations can produce gravel concretion or honeycomb especially at the corners.

Was the gravel´s maximum diameter choice correct for the structure? Due to significant presence of reinforcement the risk of “blocking” is quite high if the gravel´s maximum diameter is too high. Moreover, if the concrete cover is not thick enough and/or if reinforcement bars are bind together as for example in the links between pillars at different floors, it will be harder for the concrete to keep its homogeneity and most likely only sand and cement will flow through.
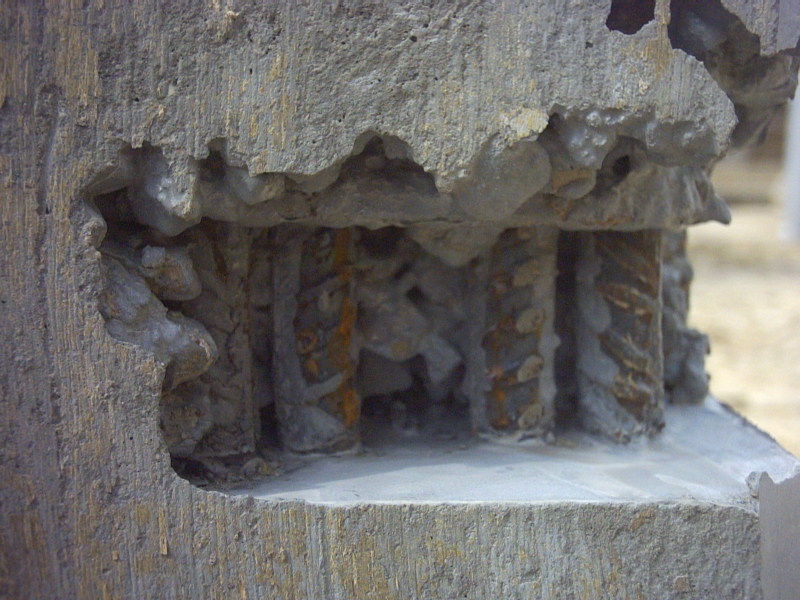
Must be added that if concrete falls from an excessive height, segregation will be the inevitable result. So, it is always advisable to “help” the concrete being poured as close as possible to its final destination. That can be done by means of a concrete pump, a pipe or a provisional ramp. The concrete free fall should not exceed 50 cm. and only SCC (please read my post “Self compacting concrete”) can flow from one single pouring point for several meters without segregation. All other types of concrete must be “helped” reaching every corner using the abovementioned tools.
IS A PATCH THE SOLUTION?
The gravel concretion or honeycomb is a weak point through which aggressive agents can infiltrate more quickly transported by air or water (please check my post "Concrete durability"). If reinforcement will remain uncovered its corrosion will be inevitable and fast. Honeycomb is also a weak point which expose the entire structure to stress not considered in the design phase. Therefore, the answer is: NO! A patch is definitely not a solution.
Commentaires